The ASM Chip Placer CA4 is a high-precision, high-speed chip placement machine based on the SIPLACE X S series, especially for semiconductor companies. The device dimensions are 1950 x 2740 x 1572 mm and weighs 3674 kg. Power requirements include 3 x 380 V~ to 3 x 415 V~±10%, 50/60 Hz, and air supply requirements are 0.5 MPa - 1.0 MPa.
Technical Parameters
Chip Placer Type: C&P20 M2 CPP M, placement accuracy ±15 μm at 3σ.
Chip Placer Speed: 126,500 components can be placed per hour.
Component size range: from 0.12 mm x 0.12 mm (0201 metric) to 6 mm x 6 mm, and from 0.11 mm x 0.11 mm (01005) to 15 mm x 15 mm.
Maximum component height: 4 mm and 6 mm.
Standard placement pressure: 1.3 N ± 0.5N and 2.7 N ± 0.5N.
Station capacity: 160 tape feeder modules.
PCB size range: from 50 mm x 50 mm to 650 mm x 700 mm, PCB thickness range from 0.3 mm to 4.5 mm.
The advantages of the ASM SIPLACE CA4 chip mounter mainly include the following aspects:
High-precision placement: The ASM SIPLACE CA4 uses a unique digital imaging system and intelligent sensors to ensure the consistency and reliability of product quality, which is essential for the production of electronic products that require high-precision components.
Ultra-high-speed placement capability: The placement machine is known for its ultra-high-speed placement, with a placement speed of up to 200,000CPH, which greatly improves production efficiency and meets the high requirements of modern production lines for speed and efficiency.
Modular design: The ASM SIPLACE CA4 adopts a modular design. The cantilever module can be flexibly configured according to production needs, providing options of 4, 3 or 2 cantilevers, thus forming different styles of placement equipment. This design not only enhances the flexibility of the equipment, but also can be customized according to the specific needs of the production line to maximize production efficiency.
Intelligent feeding system: The placement machine is equipped with an intelligent feeding system that can support components of various specifications and automatically adjust the feeding according to production needs, reducing manual intervention and further improving production efficiency
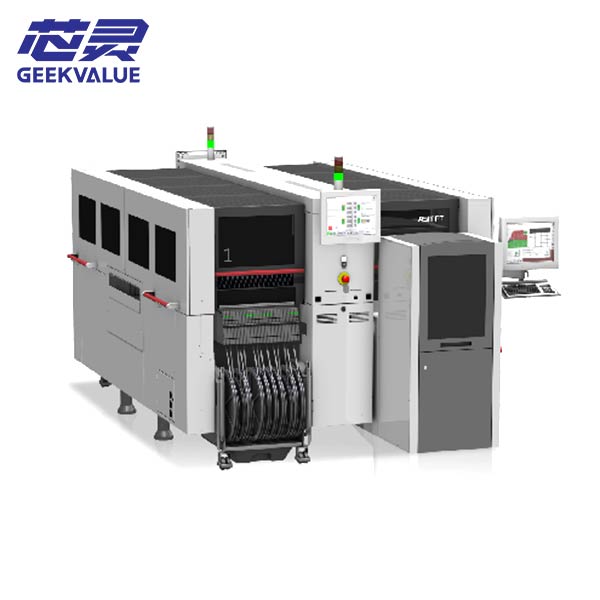